智能工厂
智能工厂
发布日期:2022-01-04
摘抄腾讯新闻,网址:https://new.qq.com/rain/a/20200729A0VHM500
工业互联网的时代已经到来,
第四次工业革命的目标是工厂智能化
基于信息融合,大数据、物联网等
实现智能制造
那么智能工厂
如何实现数据的智能采集与处理?
数据自动和智能采集系统是现场自动化控制设备与管理层之间的信息纽带,工厂中设备众多、接口各异,如何实现设备和仪表通讯就成为实施难点。
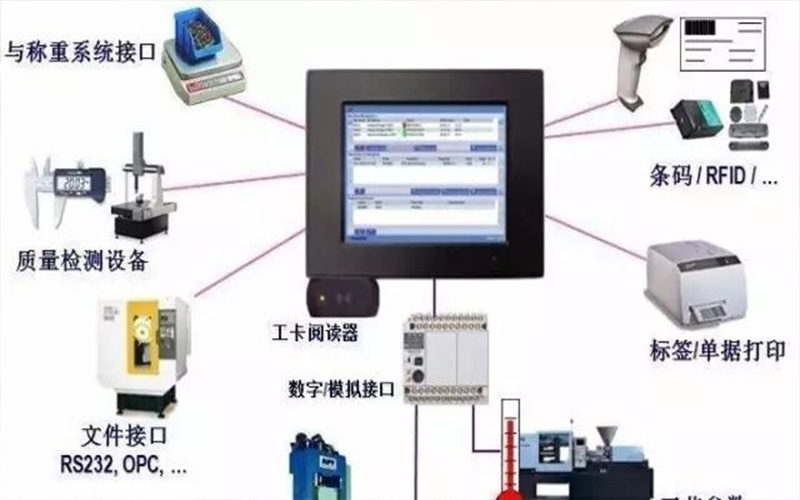
实施MES的一个技术基础就是与现场设备进行通讯,实现数据的自动化采集甚至智能采集。本文从一般性设备通讯入手,给大家介绍下工厂的数采通讯方案。
对于大部分行业,基本都可以分为前处理和包装两个工艺过程,基本的设备状况如下:
前处理控制系统属于过程控制系统,前处理设备的控制系统普遍采用了现场总线技术,形成分散控制、集中管理和监控的管控一体化模式,数据采集难度较低。
包装设备控制系统属于运动控制系统,包装设备供应厂商较多,很多设备采用专用控制器,技术不开放,数据采集接口复杂,是数据采集的难点。
质量检测仪器设备相关接口比较简单、原始,一般的检测仪器配有串口用于输出测试数据,只要仪器厂商提供通信协议,就可以实施检测仪器的数据采集。
一般工厂的动力仪表以机械式仪表居多,需要改造为智能仪表才能通讯。
3.1.控制通讯
PLC/DCS通过工业以太网接入,实现设备层的数据采集,基本的优先级如下:中控系统>操作面板>PLC网口>PLC串口,具体的建议如下:
1、控制系统采用工业以太网通信,对于不能采用工业以太网通信的,可采用Modbus RTU通信,并转换为工业以太网通讯。
2、优先从中控系统的上层软件系统中读取数据,也可以通过直接驱动从底层控制系统中读取。
3、已有以太网接口的PLC控制系统,如果可以新增以太网接口的,可通过新增以太网接口,采用工业以太网接入。
4、对于无以太网接口,但可以新增以太网口的系统,通过新增以太网口,采用工业以太网接入。
5、对于不能扩展以太网接口,但可以增加Modbus RTU通讯接口的设备,可增加Modbus通讯接口,通过串口通讯将数据先采集到新增的数采PLC,再通过PLC的以太网接口上传系统。新增的数采PLC要求配有以太网接口和Modbus串口。
6、不具备通讯采集能力的控制系统,可考虑将现有控制系统更换成带通讯接口的控制系统以实现数据采集。
7、如果现有系统设备没有PLC控制系统,则需要对现有设备控制系统进行升级改造,改造成带通讯接口的PLC控制系统进行控制,然后才能实现数据的自动采集。
注意事项:
已有以太网接口的PLC控制系统,如果采用现有以太网接口通讯,需要先修改与此连接的以太网设备的IP地址,再采用工业以太网接入。涉及到要修改IP地址的设备可能会有PLC控制系统、触摸屏、上位监控计算机、变频器、伺服驱动器等。
3.1.1.智能仪表通讯
智能仪表的通讯方案如下:
1、仪表要求为带标准的Modbus RTU通讯接口的智能仪表。如果现场的计量仪表是指针式机械表,需要将其先更换为智能仪表。
2、配有Modbus RTU接口的智能仪表先通过RS485屏蔽电缆连接,然后通过Modbus转 Modbus TCP/ IP网关转换后接入系统。智能仪表可分区域分类型连接(例如:同一区域电表接电表,水表接水表,不要混接)。为保证数据通讯的稳定性和数据传输的实时性,一条通讯总线上连接的仪表数量不要超过10个。
3.1.2.质检仪器通讯
质检仪器设备的通讯以串口/并口和文件交互方式居多
3.1.3.智能采集系统
在CPS体系中对于设备的自感知可以改变现有的被动式采集,从而实现智能化与自主化数据采集。自主式和应激式传感采集主要体现三个方面:
1、以事件为导向的采集策略。根据不同的规则进行数据采集,当设备在稳定工况下可以按照较低的频率采集。而在变化的工况下,则采用高频率的并增大数据采集范围,以便及时把握可能出现的风险。
2、以活动目的为导向的采集策略。当CPS怀疑某一关键部件出现状态异常,为了确认和诊断该故障,与此部件相关的传感器将提高采集频率。
3、以设备健康为导向的采集策略。在系统判断设备健康状态正常时,以较低的采集间隔和采集频率,采集部分数据源的数据,实现及时发现设备健康状态变化。只有在出现异常时才对故障诊断所需数据进行采集,缩短数据采集间隔,以便更加准确和及时把握设备健康状态的变化态势。
一个典型的智能数据采集管理系统是根据事件信息、活动目标和设备状态自动产生符合信息分析需求的数据采集控制信息,并将此信息传输到数采设备控制传感器的信息采集部分,通过运算逻辑、机理模型、操作原理、运行目的、信号处理等要求的控制模型,调取所需数据。
工业互联网的时代已经到来,
第四次工业革命的目标是工厂智能化
基于信息融合,大数据、物联网等
实现智能制造
那么智能工厂
如何实现数据的智能采集与处理?
数据自动和智能采集系统是现场自动化控制设备与管理层之间的信息纽带,工厂中设备众多、接口各异,如何实现设备和仪表通讯就成为实施难点。
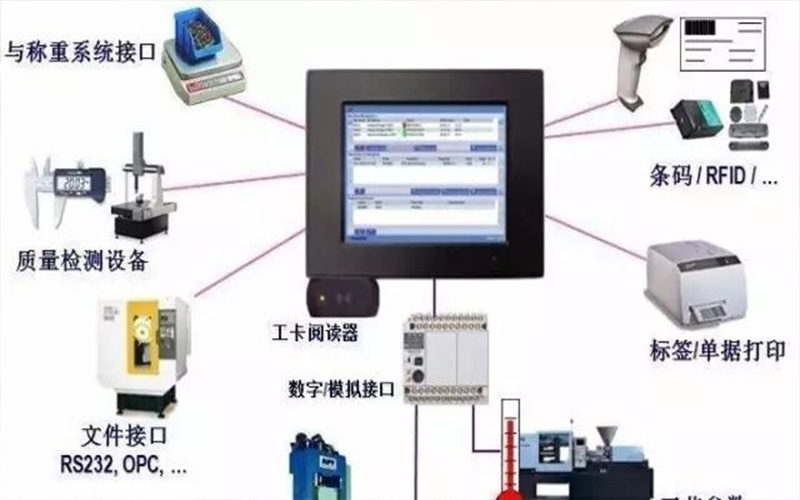
对于大部分行业,基本都可以分为前处理和包装两个工艺过程,基本的设备状况如下:
前处理控制系统属于过程控制系统,前处理设备的控制系统普遍采用了现场总线技术,形成分散控制、集中管理和监控的管控一体化模式,数据采集难度较低。
包装设备控制系统属于运动控制系统,包装设备供应厂商较多,很多设备采用专用控制器,技术不开放,数据采集接口复杂,是数据采集的难点。
质量检测仪器设备相关接口比较简单、原始,一般的检测仪器配有串口用于输出测试数据,只要仪器厂商提供通信协议,就可以实施检测仪器的数据采集。
一般工厂的动力仪表以机械式仪表居多,需要改造为智能仪表才能通讯。
3.1.控制通讯
PLC/DCS通过工业以太网接入,实现设备层的数据采集,基本的优先级如下:中控系统>操作面板>PLC网口>PLC串口,具体的建议如下:
1、控制系统采用工业以太网通信,对于不能采用工业以太网通信的,可采用Modbus RTU通信,并转换为工业以太网通讯。
2、优先从中控系统的上层软件系统中读取数据,也可以通过直接驱动从底层控制系统中读取。
3、已有以太网接口的PLC控制系统,如果可以新增以太网接口的,可通过新增以太网接口,采用工业以太网接入。
4、对于无以太网接口,但可以新增以太网口的系统,通过新增以太网口,采用工业以太网接入。
5、对于不能扩展以太网接口,但可以增加Modbus RTU通讯接口的设备,可增加Modbus通讯接口,通过串口通讯将数据先采集到新增的数采PLC,再通过PLC的以太网接口上传系统。新增的数采PLC要求配有以太网接口和Modbus串口。
6、不具备通讯采集能力的控制系统,可考虑将现有控制系统更换成带通讯接口的控制系统以实现数据采集。
7、如果现有系统设备没有PLC控制系统,则需要对现有设备控制系统进行升级改造,改造成带通讯接口的PLC控制系统进行控制,然后才能实现数据的自动采集。
注意事项:
已有以太网接口的PLC控制系统,如果采用现有以太网接口通讯,需要先修改与此连接的以太网设备的IP地址,再采用工业以太网接入。涉及到要修改IP地址的设备可能会有PLC控制系统、触摸屏、上位监控计算机、变频器、伺服驱动器等。
3.1.1.智能仪表通讯
智能仪表的通讯方案如下:
1、仪表要求为带标准的Modbus RTU通讯接口的智能仪表。如果现场的计量仪表是指针式机械表,需要将其先更换为智能仪表。
2、配有Modbus RTU接口的智能仪表先通过RS485屏蔽电缆连接,然后通过Modbus转 Modbus TCP/ IP网关转换后接入系统。智能仪表可分区域分类型连接(例如:同一区域电表接电表,水表接水表,不要混接)。为保证数据通讯的稳定性和数据传输的实时性,一条通讯总线上连接的仪表数量不要超过10个。
3.1.2.质检仪器通讯
质检仪器设备的通讯以串口/并口和文件交互方式居多
3.1.3.智能采集系统
在CPS体系中对于设备的自感知可以改变现有的被动式采集,从而实现智能化与自主化数据采集。自主式和应激式传感采集主要体现三个方面:
1、以事件为导向的采集策略。根据不同的规则进行数据采集,当设备在稳定工况下可以按照较低的频率采集。而在变化的工况下,则采用高频率的并增大数据采集范围,以便及时把握可能出现的风险。
2、以活动目的为导向的采集策略。当CPS怀疑某一关键部件出现状态异常,为了确认和诊断该故障,与此部件相关的传感器将提高采集频率。
3、以设备健康为导向的采集策略。在系统判断设备健康状态正常时,以较低的采集间隔和采集频率,采集部分数据源的数据,实现及时发现设备健康状态变化。只有在出现异常时才对故障诊断所需数据进行采集,缩短数据采集间隔,以便更加准确和及时把握设备健康状态的变化态势。
一个典型的智能数据采集管理系统是根据事件信息、活动目标和设备状态自动产生符合信息分析需求的数据采集控制信息,并将此信息传输到数采设备控制传感器的信息采集部分,通过运算逻辑、机理模型、操作原理、运行目的、信号处理等要求的控制模型,调取所需数据。
推荐精彩博文